A storage box mould is a specialized injection mold designed for manufacturing plastic storage boxes used in homes, offices, warehouses, and more. Crafted from high-grade steel, the mould is built for durability and high-volume production, ensuring that each storage box produced has precise dimensions, a smooth finish, and excellent durability. It can be customized to produce storage boxes in various shapes, sizes, and styles, including boxes with lids, compartments, or stackable designs.
The mould’s advanced design includes efficient cooling systems to speed up the production cycle, maintaining quality while improving output. Ideal for producing sturdy, lightweight storage boxes for organizing and storing items, the mould ensures a seamless production process with attention to detail, from reinforced corners to easy-to-grip handles. Customization options are available to meet specific design and branding needs, making it a versatile tool for various industries.
Basic Information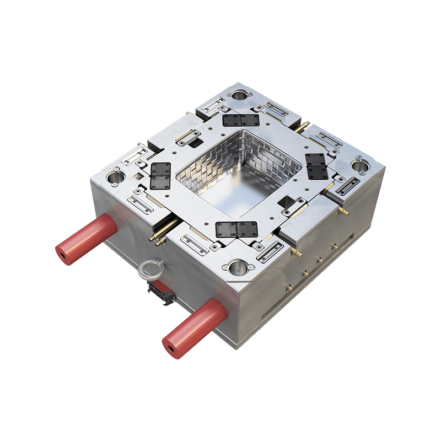
Mold Type: Storage Box Mould
Mold Material Options:P20, 718, 738, NAK80, S136
Mold Base Standards: HASCO, DME, MISUMI, JIS, LKM, etc.
Mold Runner System:Cold Runner / Hot Runner
Mold Gate Options:Slide Gate, Sub Gate, Pin-point Gate
Cavity:Single or Multi-Cavity
Design Software Supported:UG, PROE, CAD, SOLIDWORKS
Molding Equipment Used:CNC, Wire Cutting, Milling Machine, EDM
Compatible Raw Materials:ABS, PP, PC, PA6, PA66, PVC, POM, PMMA, PS, etc.
Packaging Method:Wooden pallet or carton
OEM Services:Available—please provide 2D/3D files or samples
Lead Time:Approximately 30 days
OEM Services for Molds
– Custom Design: Develop bespoke designs based on client specifications, including detailed technical drawings and 3D models.
– Material Selection: Assist clients in choosing the right materials for both the mold and the end product to ensure durability and performance.
– Tooling Development: Design and manufacture custom tooling and molds tailored to specific production needs and technical requirements.
– Prototype Creation: Produce prototypes for client review to verify design accuracy and functionality before proceeding with mass production.
– Precision Machining: Utilize advanced machining techniques, including CNC and EDM, to create high-precision molds.
– Surface Treatment: Apply various surface finishes, such as polishing, coating, and texturing, to meet aesthetic and functional specifications.
– Testing and Validation: Conduct thorough testing of molds to ensure they meet performance standards and client requirements.
– Iterative Refinements: Make necessary adjustments based on testing results and client feedback to optimize mold performance.
– Production Support: Provide ongoing support throughout the production process, including troubleshooting and adjustments.
– Quality Assurance: Implement rigorous quality control procedures to ensure all molds meet industry standards and client specifications.
– Logistics and Delivery: Manage the delivery process to ensure timely and secure shipment of molds to client facilities.
– After-Sales Support: Offer comprehensive after-sales support, including maintenance and modifications, to ensure continued satisfaction and performance.