Our cutting-edge plastic insert molding solutions for new energy applications. Our advanced molds are designed to deliver exceptional quality, meeting stringent customization requirements and enabling high-volume production with rapid prototyping capabilities. The precision-engineered molds are perfect for producing durable, reliable components essential for the latest new energy systems. With a focus on high performance and flexibility, our plastic insert molding solutions ensure efficient production processes, from tailored prototypes to extensive manufacturing runs. Experience superior quality and customization with our state-of-the-art plastic insert molding technology.
Basic Information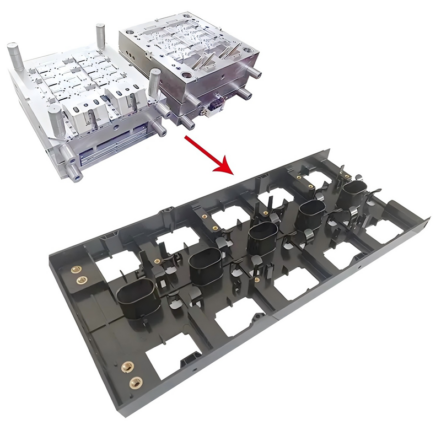
Mold Type: Plastic Insert Mold
Mold Material Options:P20, 718, 738, NAK80, S136
Mold Base Standards: HASCO, DME, MISUMI, JIS, LKM, etc.
Mold Runner System:Cold Runner / Hot Runner
Mold Gate Options:Slide Gate, Sub Gate, Pin-point Gate
Cavity:Single or Multi-Cavity
Design Software Supported:UG, PROE, CAD, SOLIDWORKS
Molding Equipment Used:CNC, Wire Cutting, Milling Machine, EDM
Compatible Raw Materials:ABS, PP, PC, PA6, PA66, PVC, POM, PMMA, PS, etc.
Packaging Method:Wooden pallet or carton
OEM Services:Available—please provide 2D/3D files or samples
Lead Time:Approximately 30 days
Customization Service for Molds
– Design Consultation:Collaborate with clients to understand specific design requirements and preferences.
– Technical Drawings:Create detailed technical drawings and specifications based on client input.
– Material Selection:Assist in choosing appropriate materials for both the mold and the final product to ensure optimal performance.
– Tooling Development:Develop custom tooling and molds tailored to meet precise specifications and production needs.
– Prototype Production:Produce prototypes to validate design, functionality, and material choices before full-scale production.
– Mold Fabrication:Utilize advanced manufacturing techniques to create high-quality, durable molds.
– Surface Finishing:Apply various surface treatments, including polishing, coating, and texturing, to meet aesthetic and functional requirements.
– Testing and Validation:Conduct rigorous testing of molds to ensure they meet quality standards and performance expectations.
– Adjustments and Iterations: Make necessary adjustments and refinements based on prototype testing and client feedback.
– Production Support:Provide ongoing support throughout the production process, including troubleshooting and maintenance.
– Quality Assurance: Implement stringent quality control measures to ensure the molds meet industry standards and client specifications.
– Delivery and Installation:Manage logistics for timely delivery and offer installation support to ensure seamless integration into the production line.