Household Mould Injection Mold Tooling refers to specialized molds used in the injection molding process to produce various household items. These tools ensure accurate shaping, high durability, and mass production efficiency. Common applications include kitchenware, storage containers, and home appliance components. Precision design and robust construction make them essential for consistent product quality in the home goods industry.
Basic Information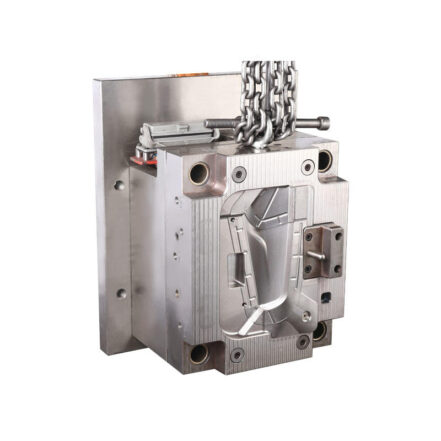
Mold Type: Plastic Injection Mold
Mold Material Options:P20, 718, 738, NAK80, S136
Mold Base Standards: HASCO, DME, MISUMI, JIS, LKM, etc.
Mold Runner System:Cold Runner / Hot Runner
Mold Gate Options:Slide Gate, Sub Gate, Pin-point Gate
Cavity:Single or Multi-Cavity
Design Software Supported:UG, PROE, CAD, SOLIDWORKS
Molding Equipment Used:CNC, Wire Cutting, Milling Machine, EDM
Compatible Raw Materials:ABS, PP, PC, PA6, PA66, PVC, POM, PMMA, PS, etc.
Packaging Method:Wooden pallet or carton
OEM Services:Available—please provide 2D/3D files or samples
Lead Time:Approximately 30 days
Quality Control Process
-
Sales Department (RFQ – Request for Quotation)
– Receive and process initial customer inquiries and Requests for Quotation (RFQs). Evaluate the project’s scope and requirements to prepare accurate and competitive quotes.
-
Project Department (Quotation)
– Develop detailed and comprehensive quotations based on the RFQ received. Ensure that all aspects of the project, including materials, labor, and delivery, are accurately represented in the quote.
-
Sales Department (PO – Purchase Order)
– Confirm receipt of the Purchase Order (PO) from the client. Verify order details and initiate the project workflow.
-
Project/Engineering Department (Part Analysis)
– Conduct an in-depth analysis of the parts and components required for the project. This includes evaluating design specifications, material requirements, and production feasibility.
-
Project/Engineering Department (Approval)
– Obtain approval for the project from relevant stakeholders. Ensure all design and material specifications are confirmed before proceeding.
-
Project/Engineering Department (Drawing/Order Material)
– Finalize and approve detailed drawings and material orders. Ensure that all drawings are accurate and that the materials ordered match project requirements.
-
Project/Engineering Department (Punching Process Control)
– Oversee the punching process to ensure that all components are manufactured to precise specifications. Implement process controls to maintain consistency and quality.
-
Project/Engineering Department (Sheet Quotation)
– Review and approve quotations for sheet materials used in the project. Ensure that all materials meet quality standards and are cost-effective.
-
Sales Department (Order Review)
– Conduct a final review of the order details, including quantities, specifications, and delivery timelines. Confirm all information before proceeding to production.
-
Project/Engineering Department (Project Approval Form)
– Complete and approve the Project Approval Form, which includes finalizing project timelines, budgets, and resource allocation.
-
Project/Engineering Department (Drawing)
– Prepare and finalize production drawings. Ensure that all drawings are detailed and accurate for use in manufacturing.
-
Project/Engineering Department (Project Schedule)
– Develop a comprehensive project schedule, outlining key milestones, deadlines, and resource requirements. Monitor progress to ensure adherence to the schedule.
-
Project/Engineering Department (To T1)
– Proceed to the T1 trial phase, where initial prototypes or samples are produced. Evaluate the trial results for any necessary adjustments.
-
Project/Engineering Department (Trial Modification)
– Implement modifications based on the trial results. Address any issues identified during the trial phase to ensure that the final product meets quality standards.
-
Sales/Project/Engineering Departments (Goods Delivery)
– Oversee the final delivery of goods to the client. Ensure that all products are delivered on time, meet quality standards, and are accompanied by the necessary documentation.
This structured approach ensures rigorous quality control throughout the entire process, from initial quotation to final delivery, maintaining high standards and client satisfaction.
Factory Show
Our 4,500㎡ factory boasts over 20 years of OEM expertise and is equipped with world-class machinery, including Roders, Makino, Sodick, and YCM. Leveraging advanced tooling technology, we achieve micron-level precision in tool manufacturing. With ARBURG, Miltitech, and 2KM equipment, we produce ultra-precision components as small as 0.02g and as thin as 0.1mm. Our ISO-certified Class 8 medical-grade dust-free workshop ensures a controlled environment for high-quality medical device components.