Overview
Plastic Plates and Cups Molds are precision-engineered tools used in the manufacturing of disposable plastic plates and cups. These molds are designed to produce high-quality, consistent products in various shapes, sizes, and designs, suitable for foodservice, catering, and packaging industries. Made from durable materials, plastic molds ensure efficient production with minimal defects, allowing for high-volume output while maintaining product integrity. The molds are designed for ease of use in injection molding or thermoforming processes, delivering cost-effective solutions for creating lightweight, sturdy, and environmentally responsible plastic plates and cups.
Basic Information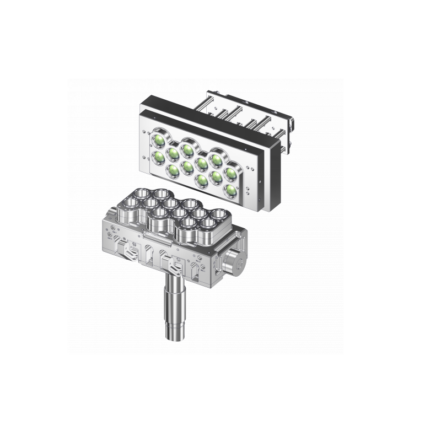
Mold Type: Plastic Injection Mold
Mold Material Options:P20, 718, 738, NAK80, S136
Mold Base Standards: HASCO, DME, MISUMI, JIS, LKM, etc.
Mold Runner System:Cold Runner / Hot Runner
Mold Gate Options:Slide Gate, Sub Gate, Pin-point Gate
Cavity:Single or Multi-Cavity
Design Software Supported:UG, PROE, CAD, SOLIDWORKS
Molding Equipment Used:CNC, Wire Cutting, Milling Machine, EDM
Compatible Raw Materials:ABS, PP, PC, PA6, PA66, PVC, POM, PMMA, PS, etc.
Packaging Method:Wooden pallet or carton
OEM Services:Available—please provide 2D/3D files or samples
Lead Time:Approximately 30 days
Customization Service for Molds
– Design Consultation:Collaborate with clients to understand specific design requirements and preferences.
– Technical Drawings:Create detailed technical drawings and specifications based on client input.
– Material Selection:Assist in choosing appropriate materials for both the mold and the final product to ensure optimal performance.
– Tooling Development:Develop custom tooling and molds tailored to meet precise specifications and production needs.
– Prototype Production:Produce prototypes to validate design, functionality, and material choices before full-scale production.
– Mold Fabrication:Utilize advanced manufacturing techniques to create high-quality, durable molds.
– Surface Finishing:Apply various surface treatments, including polishing, coating, and texturing, to meet aesthetic and functional requirements.
– Testing and Validation:Conduct rigorous testing of molds to ensure they meet quality standards and performance expectations.
– Adjustments and Iterations: Make necessary adjustments and refinements based on prototype testing and client feedback.
– Production Support:Provide ongoing support throughout the production process, including troubleshooting and maintenance.
– Quality Assurance: Implement stringent quality control measures to ensure the molds meet industry standards and client specifications.
– Delivery and Installation:Manage logistics for timely delivery and offer installation support to ensure seamless integration into the production line.
Advantages of Our Mold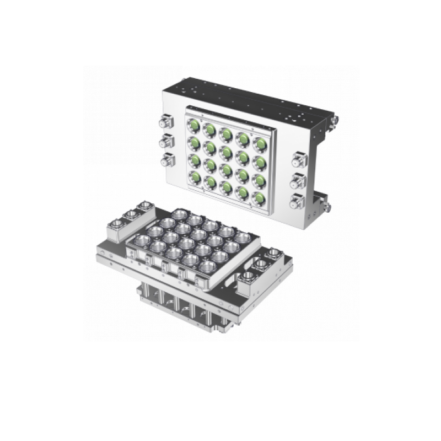
-
Superior Quality:
– Our molds are manufactured using high-grade materials and state-of-the-art techniques, ensuring exceptional durability, precision, and longevity. Each mold undergoes rigorous quality control checks to meet stringent industry standards.
-
Customization:
– We offer highly customizable mold designs tailored to meet specific client requirements. Our team works closely with clients to develop molds that align perfectly with their unique production needs and specifications.
-
Advanced Technology:
– Utilizing the latest in CNC machining, laser cutting, and precision engineering, our molds are crafted with unparalleled accuracy. Our advanced technology ensures consistent, high-quality output and reduces production downtime.
-
Rapid Prototyping:
– We provide quick turnaround times for prototypes, allowing clients to test and validate their designs swiftly. This accelerates the product development process and brings products to market faster.
Why Choose Us?
Apply changes quickly and at a low cost to materials and designs
24/7 design and engineering support
Long-lasting and high-quality surface finishing
Quick delivery of production-quality components