Our Matte Plastic LSR Overmolding Mold provides an innovative solution for producing durable silicone components with a matte finish. Engineered for precision, this mold integrates the strength of liquid silicone rubber (LSR) with a sleek, non-slip surface that reduces glare. Combining aesthetics and functionality, it is ideal for high-performance applications. Through advanced LSR injection molding and overmolding techniques, we ensure superior durability and consistent quality in every production run. We offer customization to meet specific design requirements. Get in touch with us today to explore custom solutions for your mold project!
Basic Information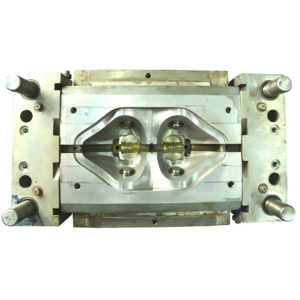
Mold Type: Plastic Injection Mold
Mold Material Options:P20, 718, 738, NAK80, S136
Mold Base Standards: HASCO, DME, MISUMI, JIS, LKM, etc.
Mold Runner System:Cold Runner / Hot Runner
Mold Gate Options:Slide Gate, Sub Gate, Pin-point Gate
Cavity:Single or Multi-Cavity
Design Software Supported:UG, PROE, CAD, SOLIDWORKS
Molding Equipment Used:CNC, Wire Cutting, Milling Machine, EDM
Compatible Raw Materials:ABS, PP, PC, PA6, PA66, PVC, POM, PMMA, PS, etc.
Packaging Method:Wooden pallet or carton
OEM Services:Available—please provide 2D/3D files or samples
Lead Time:Approximately 30 days
Surface Treatment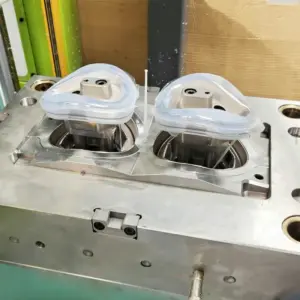
- Polishing:
This process refines the mold’s surface finish, reducing friction and improving both appearance and performance. A well-polished mold leads to high-quality, defect-free products with superior surface smoothness.
- Texturing:
Texturing involves applying intricate patterns or designs to the mold surface. It’s ideal for creating unique finishes on the final product, such as leather-like textures or fine grooves, enhancing both functionality and visual appeal.
- Hard Chrome Plating:
Hard chrome plating enhances the hardness and wear resistance of the mold. It’s particularly effective for molds subjected to high friction, ensuring prolonged tool life and consistent product quality.
- Nitriding:
Nitriding diffuses nitrogen into the steel surface of the mold, forming a hard, wear-resistant layer. This treatment is essential for molds used in high-stress applications, enhancing their durability and performance.
- Titanium Nitride (TiN) Coating:
TiN coating provides a gold-colored, hard surface that enhances wear resistance, reduces friction, and improves mold release properties, making it ideal for high-volume production runs.
- Nickel Plating:
Nickel plating offers excellent corrosion resistance, protecting the mold from chemical or environmental exposure, particularly useful for molds operating in harsh conditions.
- Electroless Nickel Plating:
This uniform coating provides enhanced hardness, wear resistance, and corrosion protection without the need for an electric current. It ensures long-lasting mold performance, even in challenging environments.
- Anodizing:
Commonly used for aluminum molds, anodizing provides a durable, corrosion-resistant surface, allowing for color customization and enhanced aesthetic quality for easy identification.
- Black Oxide Coating:
Black oxide coating improves the mold’s corrosion resistance and appearance by creating a uniform black finish. It also reduces light reflection, beneficial for certain production environments.
- PVD (Physical Vapor Deposition) Coating:
PVD applies thin, durable layers of materials such as titanium, chromium, or zirconium to the mold surface, significantly increasing wear resistance, reducing friction, and improving mold longevity.
- Matt Finish:
A matt finish reduces surface gloss, creating a non-reflective surface ideal for products requiring a subdued, textured look. This finish can enhance the overall appearance and tactile quality of the molded part.
- VDI (Verein Deutscher Ingenieure) Textures:
VDI textures are standardized surface finishes commonly used in plastic injection molding. These textures range from fine to coarse and are essential for creating desired finishes on the final product.
- SPI (Society of the Plastics Industry) Finishes:
SPI surface finishes are industry-standard grades for plastic injection molds, ranging from mirror-like finishes to rough textures. Each grade offers distinct advantages based on the application and product requirements.
- Ball Burnishing:
Ball burnishing is a surface treatment that involves the mechanical smoothing of the mold surface through the application of steel balls under pressure. This process increases the surface hardness, enhances corrosion resistance, and provides a highly polished, defect-free finish.