Custom Automatic Thread Unloading Injection Mold is a specialized tool designed for producing threaded plastic components with precision and efficiency. It features an automated unscrewing system that removes threaded parts during the ejection process, eliminating manual handling and reducing cycle time. Custom designs allow for tailored specifications, including thread size, part geometry, and mold cavity configurations, ensuring optimal performance for various industrial applications such as automotive, packaging, and consumer goods manufacturing.
Basic Information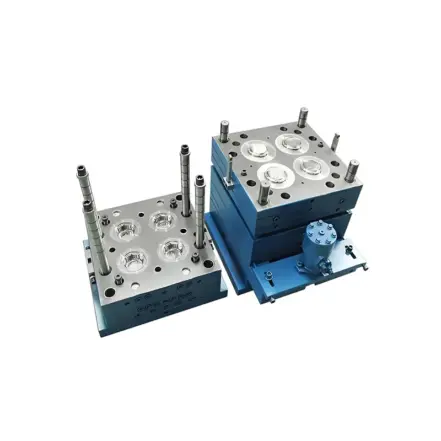
Mold Type: Automatic Thread Unloading Injection Mold
Mold Material Options:P20, 718, 738, NAK80, S136
Mold Base Standards: HASCO, DME, MISUMI, JIS, LKM, etc.
Mold Runner System:Cold Runner / Hot Runner
Mold Gate Options:Slide Gate, Sub Gate, Pin-point Gate
Cavity:Single or Multi-Cavity
Design Software Supported:UG, PROE, CAD, SOLIDWORKS
Molding Equipment Used:CNC, Wire Cutting, Milling Machine, EDM
Compatible Raw Materials:ABS, PP, PC, PA6, PA66, PVC, POM, PMMA, PS, etc.
Packaging Method:Wooden pallet or carton
OEM Services:Available—please provide 2D/3D files or samples
Lead Time:Approximately 30 days
Mould Manufacturing Process
– Inquiry Reception
– Receive customer inquiries promptly.
– Quotation and Details
– Provide price offers or detailed information within 16 hours.
– Drawing Submission
– Customers provide 2D/3D drawings and additional mold details.
– Order Confirmation
– Confirm order details including quality, price, material, delivery time, payment terms, etc.
– Production Preparation
– Prepare for production according to client’s requirements.
– Mold Detail Confirmation
– Clients confirm the specific details of the mold.
– Surface Shaping
– Perform operations such as drilling holes, high-speed carving, wire cutting, EDM, etc.
– Sample Testing
– Arrange for test mold production and send samples to customers for evaluation.
– Feedback and Adjustments
– If clients are not satisfied with the samples, provide feedback for adjustments.
– Repair and Finishing
– Conduct repairs, polishing, and texture application as necessary.
– Sample Approval
– Send revised samples until customers’ confirmation is obtained.
– Delivery
– Arrange delivery by sea, air, etc., as per customer preference.
Factory Show
Our 4,500㎡ factory boasts over 20 years of OEM expertise and is equipped with world-class machinery, including Roders, Makino, Sodick, and YCM. Leveraging advanced tooling technology, we achieve micron-level precision in tool manufacturing. With ARBURG, Miltitech, and 2KM equipment, we produce ultra-precision components as small as 0.02g and as thin as 0.1mm. Our ISO-certified Class 8 medical-grade dust-free workshop ensures a controlled environment for high-quality medical device components.