What is Mold Tooling?
Mold tooling is a critical manufacturing process involving the use of metal molds to shape molten plastic resins. The term "tooling" refers to the metal mold used in injection molding, and "mold" and "tooling" are often used interchangeably. Mold tooling can also describe the process of machining a mold from a solid block of metal, where a core and cavity are cut to create the negative shape of the part.
During the injection molding process, the mold is securely clamped by the molding machine. Molten plastic is injected into the mold at high pressure. After cooling, the mold opens, and the finished part is ejected. This cycle is repeated until the required number of parts is produced.
High-quality mold tooling is essential for producing precision parts. At our facility, we use premium components and materials for all our injection molding tooling. We collaborate closely with you to ensure that every project meets your specifications and delivers the highest quality results.
Mold Tooling Process
CAD Design
The foundation of any successful mold, be it for plastic injection or rubber, lies in its initial engineering design. Studies show that approximately 70% of a product's cost is determined during the design phase.
Mold Base and Accessories
Once the design is finalized, we order the mold base along with essential components such as bushings, pins, and other hardware. Hot runner systems, which offer reduced scrap rates and faster cycle times, are becoming increasingly crucial in plastic injection molding. However, these systems may have longer lead times.
Rough Machining
Upon receipt of the mold base, we commence rough machining. This step involves removing excess material to approach the final mold size, leaving a precise finish layer of 0.15mm to 0.30mm for subsequent precision machining.
Heat Treatment
Following rough machining, the mold undergoes heat treatment. This process alleviates stresses, minimizes corrosion, and enhances the longevity of the tool.
CNC Precision Machining
Combining Computer Numerical Control (CNC) machining with Computer-Aided Design (CAD) and Computer-Aided Machining (CAM) technologies ensures the creation of molds with tight tolerances.
Hard Milling
Hard milling is a critical technique for modern mold makers. By machining parts in their hardened state, this process can often eliminate the need for secondary machining steps, Electrical Discharge Machining (EDM), and hand polishing, resulting in time and cost savings. At Quest Industries, we excel in high-speed and high-performance hard milling, backed by both advanced equipment and extensive experience.
By leveraging these advanced methodologies, we ensure that every mold we produce meets the highest standards of precision and quality.
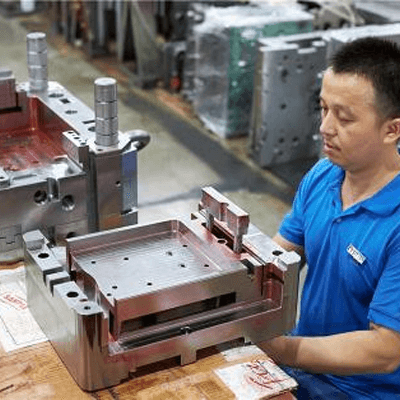
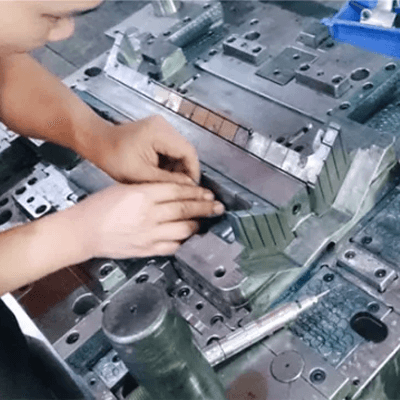
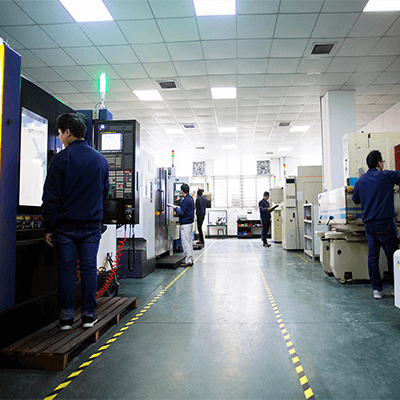
Types of Tooling
Soft Tooling
Soft tooling is typically used for producing low to medium volumes of parts. It primarily employs aluminum for mold construction, making it a cost-effective solution for prototyping or creating intricate mold patterns that might be too complex or time-consuming to produce with other methods.
However, soft tooling has limitations in terms of durability. It tends to degrade more quickly than hard tooling, which can lead to dimensional inaccuracies and increased need for replacements. As a result, soft tooling can lead to longer turnaround times and higher waste.
Hard Tooling
In contrast, hard tooling is constructed from robust metals such as steel or nickel alloys. This type of tooling is designed to endure extensive production cycles, making it ideal for high-volume manufacturing. Although the initial setup for hard tooling is more time-consuming and costly compared to soft tooling, its longevity and ability to produce a large number of parts before needing replacement make it the preferred choice for large-scale production runs.
Overall, while hard tooling involves a greater upfront investment, its durability and efficiency in high-volume production environments often outweigh the initial costs.
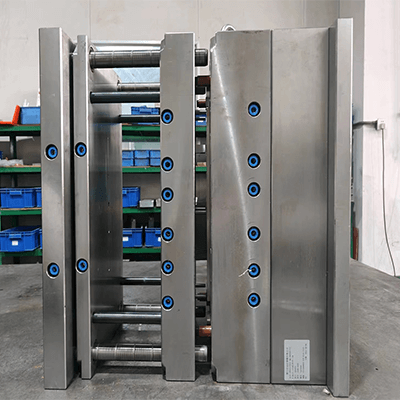
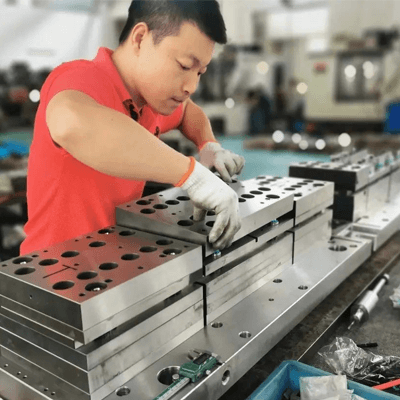
In-House Injection Molding Tool Design and Adjustments
Streamlined Tool Adjustment Process
Many injection molders rely on external tool builders for the initial creation of molds, which often results in tools that require adjustments to meet precise dimensions. This process typically involves sending the tool to a separate facility for final modifications, which can extend lead times by a month or more.
At our facility, we handle the majority of these adjustments in-house. Our approach involves a meticulous "fine-tuning" process following the initial sampling. This allows us to refine the tool's core/cavity geometry and achieve the desired dimensions without the extensive delays associated with external modifications.
Optimizing Mold Design for Manufacturability
Our primary focus in injection molding tool design is to achieve optimal manufacturability. This involves developing a high-quality mold process that is user-friendly, easy to maintain, and consistently meets customer specifications—all while minimizing costs.
Advanced EDM Capabilities
To further ensure precision in mold production, we utilize advanced Electrical Discharge Machining (EDM) technology. This process involves placing an electrode (typically made of carbon) and the mold in a dielectric fluid. A controlled electrical current is discharged between the electrode and the mold, selectively removing material from both. By adjusting the strength and duration of the current, we can achieve precise control over mold geometry, including the creation of complex three-dimensional shapes.
Our EDM capabilities include:
- OPS Ingersoll Eagle 1200 CNC RAM EDM (2016): With a maximum workpiece dimension of 50” x 60.7” x 26.8” and travel dimensions of 39.4” x 59.4” x 27.5”.
- OPS Ingersoll Eagle 800 CNC RAM EDM (2018): Featuring a maximum workpiece dimension of 31.5” x 43.3” x 18.8” and travel dimensions of 21.7” x 33.4” x 17.7”.
- Ingersoll Gantry Style 600 CNC EDM: Providing high precision for mold adjustments.
- Mitsubishi FX20K Wire EDM: Accommodating workpiece dimensions of 41.34” x 31.5” x 11.61”.
By integrating these advanced technologies with our in-house capabilities, we ensure that every mold is engineered and refined to the highest standards of precision and efficiency.