Silicone rubber compression molding is a precise manufacturing process where uncured silicone material is carefully placed into the cavity of a mold. The mold is then closed and subjected to pressure in a heated compression molding press, where the silicone undergoes vulcanization, solidifying into the intended shape. While this process is generally slower compared to injection molding, it is particularly advantageous for prototyping or research and development (R&D) due to its relatively lower initial tooling costs. The use of multi-cavity molds can further enhance cost efficiency.
This method is highly regarded for producing silicone rubber components with intricate designs and exacting dimensional tolerances. It is especially beneficial in applications requiring complex geometries and high-quality surface finishes. Silicone rubber compression molding is widely utilized across various industries, including automotive, medical, electronics, and consumer products. It is commonly employed to manufacture items such as seals, gaskets, keypads, O-rings, and other precision parts.
Silicone Compression Molding Process
Mold Fabrication: The compression mold is precisely fabricated using CNC machining and polishing techniques. For simpler designs, a two-plate mold, comprising a cavity side and a core side, is typically employed.
Assembly and Loading: The mold plates are assembled and positioned within a compression molding machine. Silicone materials, such as High Consistency Rubber (HCR) or Liquid Silicone Rubber (LSR), are then carefully loaded into the mold.
Heating and Pressure: The machine applies controlled heat and pressure, enabling the silicone material to flow and conform to the mold cavities before solidifying.
De-molding: Once the cycle is complete, pressure is released, and the mold plates are separated to remove the formed silicone parts, concluding the molding process for standard silicone components.
At Lsrmold, we operate a variety of compression molding presses, accommodating a broad spectrum of part sizes and production requirements, from small single-cavity molds to larger multi-cavity configurations. Our versatile equipment is tailored to meet diverse manufacturing needs.
Advantages of Silicone Compression Molding:
Short Development Time: Silicone compression molding offers faster and more cost-effective tooling, leading to shorter development cycles compared to Liquid Injection Molding (LIM). This accelerates iterations and allows for quick revisions.
No Gate Vestiges: Unlike other methods, silicone compression molding parts do not have gate vestiges, as compression molds eliminate the need for gates.
Multiple Materials Application: Compression molds enable swift setup and material changes, accommodating multiple materials without messy material changeovers, unlike LIM.
Effortless De-molding and Inspection: The separation of mold plates on a nearby workbench simplifies de-molding and inspection. Compression molds can also incorporate different part designs in each cavity more easily than LIM molds.
High Efficiency of HCR: Compression molded silicone parts match the quality, surface finishes, parting lines, and flash tolerance of LSR injection molded parts. High Consistency Rubber (HCR) is efficiently molded using compression molds, whereas injection molding of HCR involves complex equipment and higher costs.
Cost-Effectiveness: Silicone compression molding streamlines insert and fabric molding processes, resulting in a simpler, faster development cycle compared to silicone LIM. Particularly suitable for micro molded parts, silicone compression molding offers reduced tooling and development time, ultimately leading to lower overall costs.
Why Choose Lsrmold for Rubber Compression Molding?
Comprehensive Manufacturing Expertise: Lsrmold stands out as a leading provider of custom rubber compression molding and gasket manufacturing within its industry segment. Our extensive capabilities include on-site rubber molding, liquid silicone rubber molding, water jet cutting, and die cutting. This broad and adaptable manufacturing skill set enables us to deliver a wide array of solutions tailored to meet diverse design challenges.
Enhanced Design Solutions: Leveraging a diverse manufacturing approach, Lsrmold is adept at addressing complex design requirements. By integrating advanced rubber molding processes with cutting-edge cutting technologies, we offer a comprehensive and flexible strategy that caters to various project demands. This ensures our clients access to a wider spectrum of innovative solutions when confronted with intricate design needs.
Versatile Production Capabilities: Our production capabilities are designed to accommodate a wide range of production volumes, from 500 to 20,000 pieces, ensuring precise attention to projects of all sizes. Additionally, our compression molding presses feature platen sizes ranging from 16" x 16" to 24" x 24", allowing us to efficiently handle parts of various dimensions and specifications.
Innovative Mold Design Partner: As a trusted partner, Lsrmold collaborates closely with clients, bringing our expertise to the forefront in delivering innovative and precise solutions. With our comprehensive manufacturing capabilities and commitment to quality, we are well-equipped to tackle even the most complex design challenges, ensuring exceptional results in rubber compression molding.
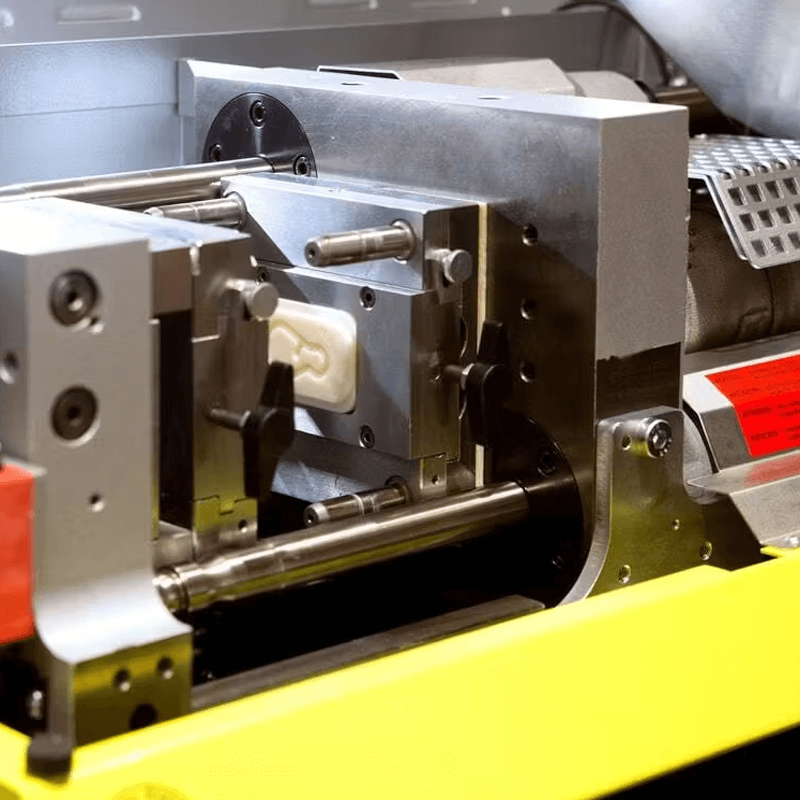
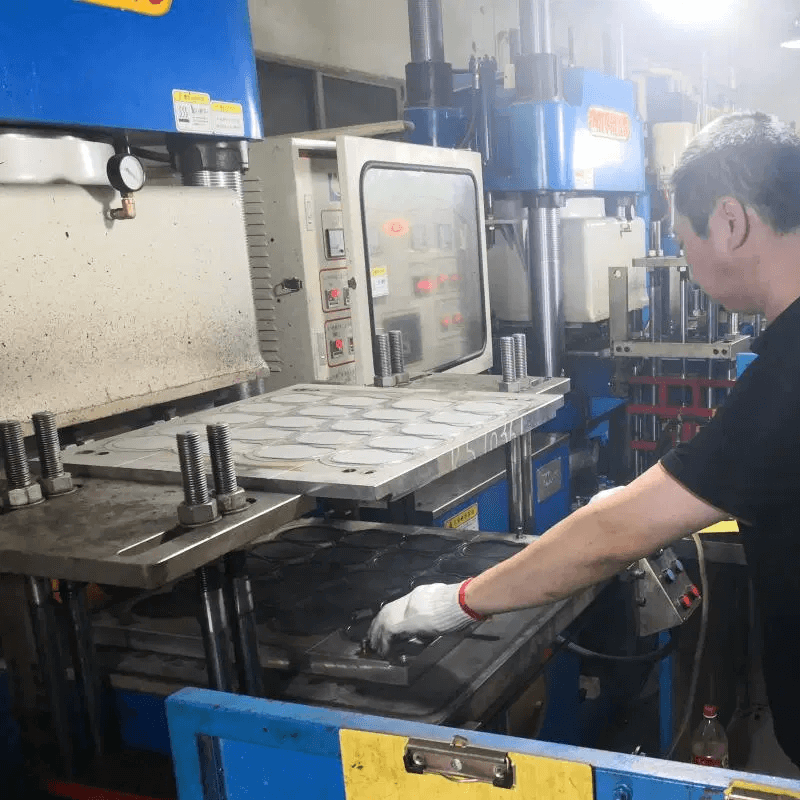
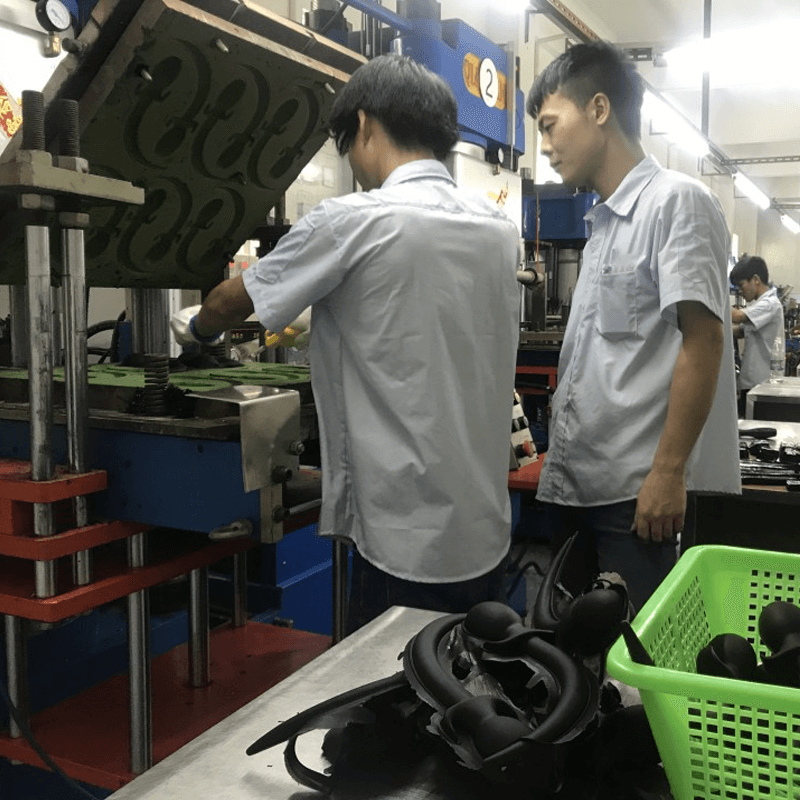
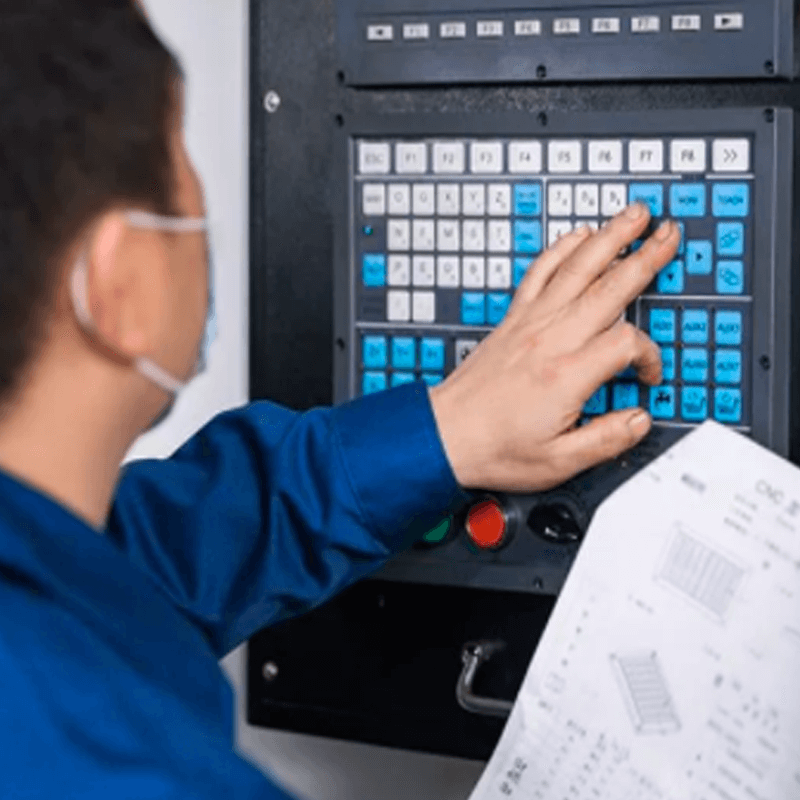
Silicone Compression Molding vs. Liquid Injection Molding
1. Cost Efficiency: Compression molds are simpler and more cost-effective than liquid injection molds. They offer cost savings and enable multi-cavity production without expensive tooling.
2. Faster Mold Creation: Compression mold fabrication takes approximately 15-20 days, and for simpler parts, only 7-10 days may suffice. In contrast, liquid injection molding requires at least 45-55 days.
3. Ease of Maintenance: The uncomplicated structure of compression molds results in easier maintenance and quicker setup of new molds. Setting up a silicone compression mold takes about 1 hour, whereas liquid silicone injection molds require approximately 1 day for assembly.
4. Versatile Material Selection: Compression molding accommodates flexible materials, allowing parts to remain pliable after curing. It can also utilize thermosets for molding multiple cavities. Common materials include silicone, natural rubber, and EPDM.
5. High Production Capacity: Compression molding machines typically offer high production capacity. Multiple-cavity compression molds yield higher output compared to injection molding.
6. Diverse Color Options: Compression molding permits testing of various colors more conveniently than liquid injection molding. Cleaning the mold and milling colored silicone for the cavity is easier. In contrast, liquid injection molds require extensive time (usually half a day) to clean the color system and needles, resulting in time and material wastage. Therefore, different colors are usually not tested using liquid injection molding.
The Manufacturing and Quality Standards for Silicone Compression Molding
Silicone compression molding in China adheres to the following manufacturing and quality standards:
- RMA Class A: Tolerances for O-ring
- ISO 3601-1: Tolerance for O-ring
- Rubber Manufacturers Association (RMA) - A2
- ISO 3601-3: Grade N and Grade S tolerances
Lsrmold, a leading mold manufacturer in China, strictly conforms to these quality standards in the production of these moldings.
With a diverse array of CNC finishing services available and our commitment to quality through rigorous inspection processes, you can be assured of receiving top-notch parts every time. Upon receiving your 3D CAD file, our experienced customer service engineers will evaluate your mold for manufacturability, ensuring it meets both your design specifications and budgetary constraints. Contact us today for a complimentary quote!