What Is Plastic Injection Molding
Plastic injection molding is a sophisticated manufacturing process for producing high-quality plastic components. This technique involves injecting molten plastic into a metal mold to create precise parts. The process starts with thermoplastic resins, which are heated until they melt and then injected into a metal mold. These molds can be constructed from materials such as steel, aluminum, or beryllium-copper alloy.
During injection molding, the molten plastic is forced into the cavity of the mold under high pressure using specialized injection molding machines, also known as presses. These machines must perform several critical functions simultaneously: melting the plastic, injecting it into the mold, and maintaining mold closure with adequate pressure, known as clamping tonnage or clamping force. For detailed information on clamping tonnage, click here. Once the plastic cools and solidifies, the mold is opened, and the finished part is ejected. The mold is then prepared for the next cycle, repeating the process to produce additional parts.
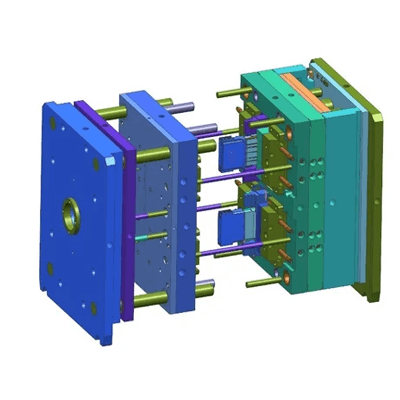
DFM (Design for Manufacturing) and Mold Flow Analysis
The Design for Manufacturing (DFM) report provides critical insights into the mold design process, including parting lines, gate types and placements, and ejector pin locations. These details are essential for client validation and ensuring that the mold design meets production requirements.
For more complex plastic parts or high-investment molds, conducting a mold flow analysis is advisable. This analysis evaluates potential molding defects and identifies optimized solutions to enhance mold performance and reliability.
The Advantages of Plastic Injection Molding
1. Enables Complex Part Designs
Plastic injection molding excels in producing complex parts with high precision. This method allows for the creation of millions of nearly identical components while maintaining exceptional quality and uniformity. To fully leverage the efficiency of high-volume molding, part designs must be optimized to balance complexity and manufacturing precision.
2. Delivers High Efficiency and Rapid Production
Injection molding is renowned for its efficiency, especially when compared to other molding methods. The process is swift, with each molding cycle lasting only 15-120 seconds depending on the complexity and size of the mold. This rapid cycle time facilitates the production of a large volume of parts within a relatively short timeframe.
3. Offers Enhanced Strength and Durability
Modern plastic injection molding utilizes advanced thermoplastics that offer strength and durability comparable to, and sometimes exceeding, that of metals. With access to over 25,000 engineered materials, including high-performance blends and hybrids, injection molding can produce parts with high tensile strength and resilience in demanding environments.
4. Provides Flexibility in Color and Material
The injection molding process offers significant flexibility in both material properties and color options. OEMs can select from a wide range of plastics and additives to meet specific project needs. This flexibility extends to the ability to produce clear or multi-colored parts, with custom color options achievable through techniques like overmolding.
5. Minimizes Waste
Injection molding is highly efficient in terms of material usage, generating minimal post-production waste. Any excess plastic, such as sprue and runners, can be regrinded and recycled for future use, contributing to a more sustainable manufacturing process.
6. Reduces Labor Costs
Labor costs associated with plastic injection molding are relatively low compared to other molding techniques. The high output rate and automated processes reduce the need for extensive manual oversight, streamlining operations and lowering overall manufacturing costs. Automated systems and self-gating tools facilitate continuous production with minimal supervision.
The Plastic Mold Manufacturing Process
1. Loading the Plastic Pellets
- Plastic resin pellets are loaded into a hopper that supplies the injection-molding machine.
2. Melting the Resin
- Pellets are gravity-fed into a heated chamber known as the barrel.
- The pellets are melted, compressed, and prepared for injection by a reciprocating screw.
3. Injection into the Mold
- The molten plastic is forced through a nozzle connected to the mold sprue bushing.
- The sprue bushing controls the material flow, directing it into the mold cavity through a gate and runner system.
4. Cooling and Solidification
- The metal mold is maintained at a lower temperature to ensure rapid solidification of the plastic.
- The plastic part cools and hardens within the mold cavity.
5. Mold Opening and Ejection
- The two mold halves, Side A and Side B (or the Cavity and Core), open.
- Ejector pins push the finished part out of the mold into a collection bin.
6. Cycle Repetition
- The mold is closed, and the process starts again for the next injection cycle.
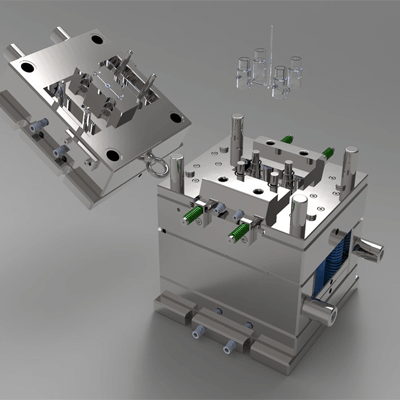
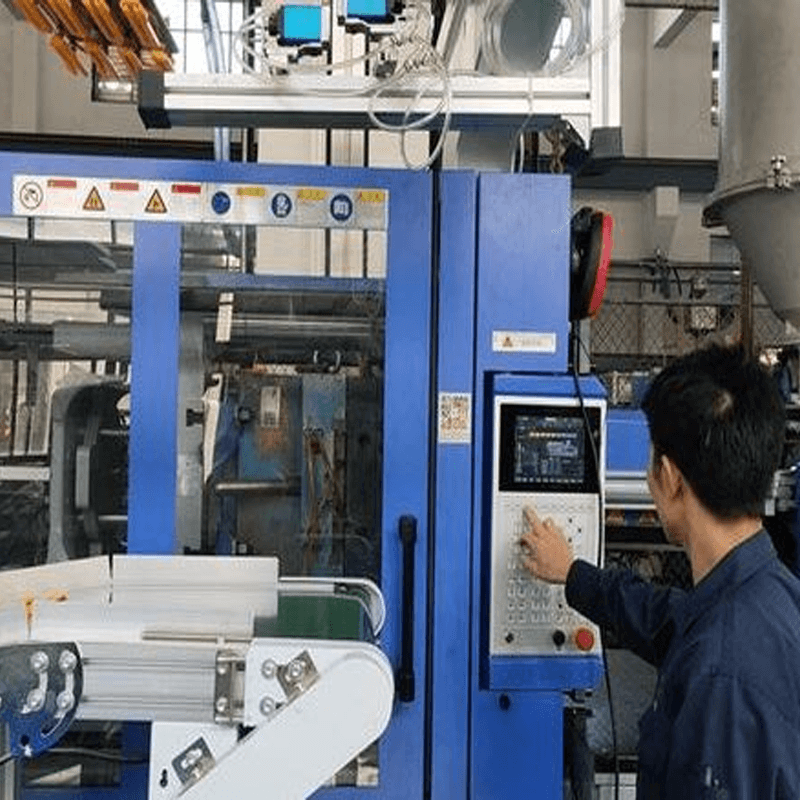
Equipment Used in the Plastic Injection Molding Process
1. Injection Molding Machines
- Description: Plastic injection molding machines, commonly known as presses, are equipped with a material hopper, a screw-type plunger, and a heating unit.
- Function: These machines clamp the mold onto the platen, where molten plastic is injected through an orifice to form the finished plastic mold.
2. Tonnage and Clamping Force
- Tonnage: Injection molding machines are rated by tonnage, which indicates the clamping force they can exert. This force is crucial for keeping the mold securely closed during the injection cycle.
- Calculation: The required tonnage depends on the part’s projected area and the material's stiffness. Typically, four to five tons of clamping force per inch are used for most projects.
3. Electric vs. Traditional Presses
- Electric Presses: Modern electric injection molding machines are preferred due to their 80% lower energy consumption and nearly 100% repeatability.
- Cost Efficiency: Although electric presses are approximately 30% more expensive than traditional presses, their cost-effectiveness is enhanced by increased production efficiency and lower operational costs.
By using advanced molding equipment, including electric presses, manufacturers ensure precision and efficiency in producing high-quality plastic molds and parts.
Why Choose Lsrmold for Your Plastic Injection Molding Needs?
Since 1998, Lsrmold has been at the forefront of plastic injection molding, delivering high-quality molds and molded parts to clients across the United States, Europe, Australia, Asia, and South America. We specialize in custom plastic injection molding for diverse industries, including medical, automotive, sports, hunting/camping, electronics, food and beverage, containers, packaging, and more.
Our custom molding process starts with an efficient online quoting system, which also provides instant quotes for CNC machined plastic prototypes. This streamlined approach ensures that you receive prompt and accurate estimates for your mold and molding needs.
At Lsrmold, we offer cost-effective custom molds and injection molded parts, typically priced 30% to 50% lower than many competitors. Our extensive experience and robust plastic injection molding expertise enable us to avoid common pitfalls, make informed decisions, and execute your projects seamlessly.
As an ISO 9001:2015 certified company, Lsrmold by Fathom adheres to rigorous quality standards, producing parts with minimal defects and delivering top-notch mold manufacturing at competitive rates.
For your next custom plastic molding project, contact Lsrmold for an instant quote or call us directly. Explore our plastic injection molding and CNC machining case studies to learn how we've successfully supported our clients and discover more about our molding capabilities.