Insert molding is a precise manufacturing process where molten plastic is injected around a substrate, such as brass threaded inserts or bushings, to create integrated components. This method allows for rapid mass production compared to machining parts entirely from metal, even though it slightly increases cycle time by about 15 seconds per insert. By combining metal inserts with plastic, the overall weight of the part can be significantly reduced.
Over-molding, a variation of insert molding, involves molding plastic around existing plastic parts to combine different materials in a single component. Lsrmold is one of the few injection molding companies that offer both insert molding and over-molding services, delivering tailored solutions for complex manufacturing challenges.
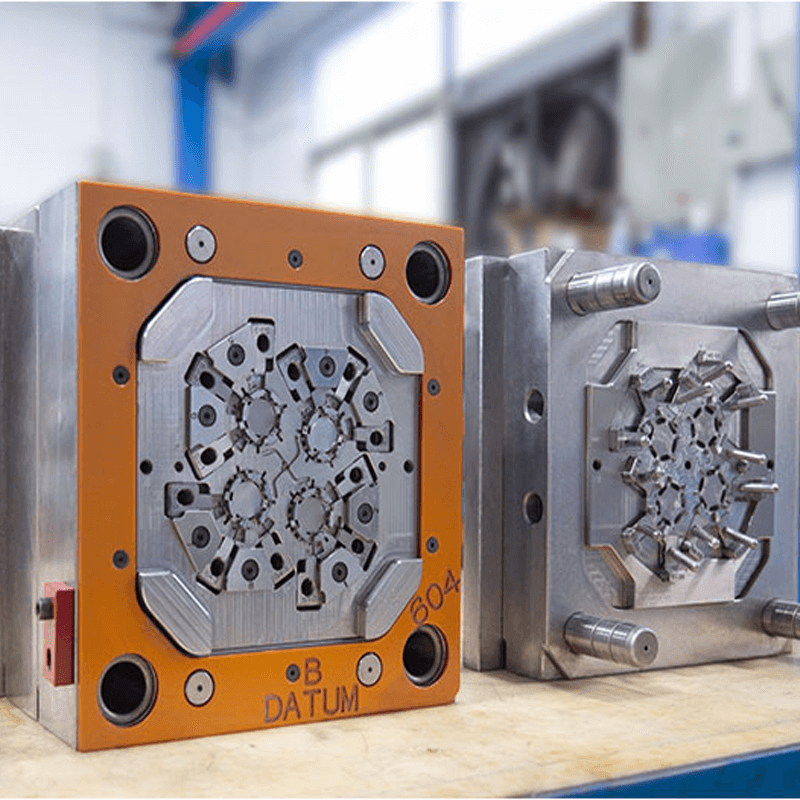
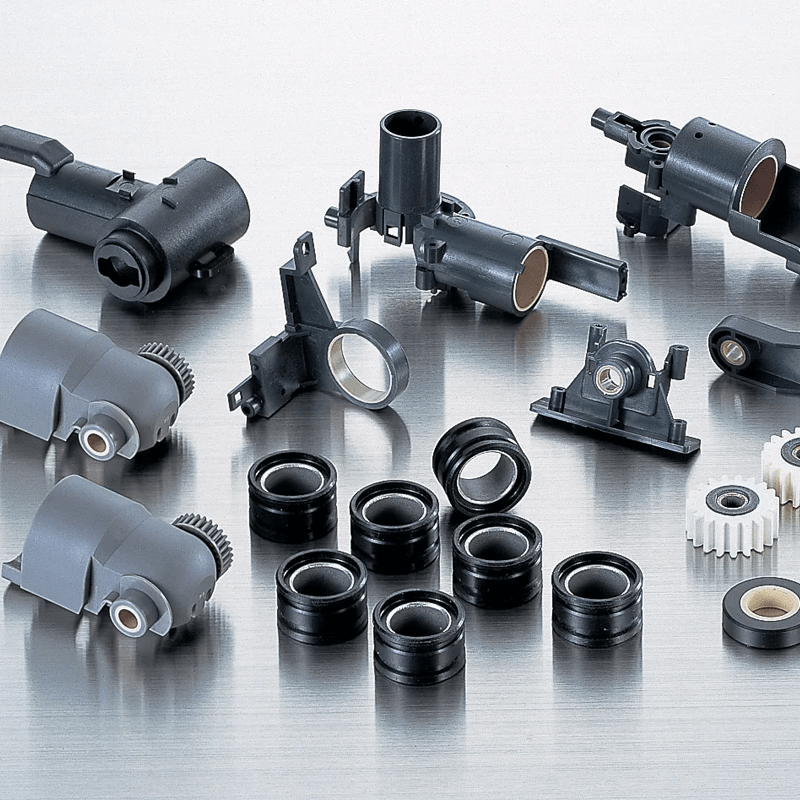
Insert Molding Services from Lsrmold
Insert molding integrates plastics and metals into a unified assembly, offering the advantage of reduced assembly and labor costs while enhancing design flexibility and part performance.
At Lsrmold, our vertical injection molding machines, equipped with rotary tables, enable precise over-molding and encapsulation of inserts for applications such as electrical circuitry, fastening, and connections. We commonly produce insert molded products like sensors, switches, connectors, and actuators.
Our insert molding presses, ranging from 55 to 300 tons, are equipped with on-press vision inspection systems that verify the correct placement of inserts. If an insert is misaligned, the system halts the press, ensuring accurate placement and safeguarding the mold from potential damage.
Lsrmold's insert molding capabilities extend to both manual and fully automated operations, complemented by secondary processes such as forming, blanking, and comprehensive hipot and continuity testing to ensure the highest quality and reliability.
Lsrmold Insert Molding Capabilities
Lsrmold offers insert molding solutions tailored to meet diverse functional and aesthetic requirements. Our approach is designed to enhance part manufacturability, reduce lead times, and improve overall part appearance. Please refer to the following standard design considerations to optimize your part's design and performance.
Standards | Metric Units | Imperial Units |
Maximum Part Size | 800×1000×400mm | 31.50×39.37×15.75in. |
Minimum Part Size | 2×2×2mm | 0.08×0.08×0.08in. |
Substrate Wall Thickness | From 0.5 to 3mm | From 0.20 to 0.12 in. |
Tolerance | +/- 0.025 mm | +/- 0.00098 in. |
Inserts | Inserts can be female and male. They both can improve a product’s appearance and utility. | |
Mold Validation | Provide T0, T1, T2 samples before mass production | |
Inspection and Certification Options | First Article Inspection, ISO 9001, ISO 13485 | |
Lead Time | From mold making to sample delivery: 15-45 business days |
Materials for Insert Molding
We offer a comprehensive selection of thermoplastic materials and inserts for custom insert molding, catering to a variety of industrial applications. Below, you'll find the materials used in custom plastic insert molding along with common examples for each.
Tooling Materials
Before commencing low or high-volume production in the insert molding process, high-precision CNC-machined tooling is essential. The most commonly used materials include:
- Tool Steel: P20, H13, S7, NAK80, S136, S136H, 718, 718H, 738
- Stainless Steel: 420, NAK80, S136, 316L, 316, 301, 303, 304
- Aluminum: 6061, 5052, 7075
Additives and Fibers
Standard plastic materials may not always meet the requirements for custom injection molding. To enhance both aesthetic and functional properties, additives and fibers can be incorporated:
- UV Absorbers
- Colorants
- Flame Retardants
- Glass Fibers
- Plasticizers
Plastic Materials
Our plastic injection molding services utilize a diverse range of materials, each offering distinct properties such as impact strength, rigidity, thermal resistance, and chemical resistance:
- ABS
- Nylon (PA)
- PC
- PVC
- PU
- PMMA
- PP
- PEEK
- PE
- HDPE
- PS
- POM
Inserts
Inserts are integrated into mold cores through manual or automated processes, allowing plastic pellets to be injected and molded around them. After the plastic hardens, the inserts are encapsulated within the finished parts. Common materials for inserts include:
- Brass
- Stainless Steel
- Aluminum
Finishing
We provide a range of finishing options to enhance products manufactured through the insert molding process. Depending on your application’s requirements, you can select from the following finishing techniques:
Finishing Options
We offer a variety of finishing options to complete your insert-molded products, tailored to meet your specific application requirements:
- Standard Finish: An interior, non-cosmetic finish applied based on the mold's geometry.
- SPI Finishes: A selection of SPI finishes ranging from Grade 3 diamond/high polish to 320 stone/low polish. Options include SPI A-1 through SPI D-3, covering various levels of surface refinement.
- Threaded Inserts: Installation of popular standard inserts in both UNF and metric sizes.
- As Molded: The part retains the original mold surface without additional texturing or polishing.
- Mold Texturing: Application of textures to the mold that appear on the final product, including matte finishes, swirls, patterns, and lines.
- Laser Engraving: Precision engraving of part numbers, designs, logos, or other specified markings.
- Pad Printing: Application of ink-based designs onto the surface of the part.
- Painting: Surface painting with standard colors or Pantone matches, including primer and topcoat options. Masking is available, and EMI (copper) paint can be applied as needed.
Insert Molding Applications
Plastic insert molding is a versatile technique used for producing prototypes and final products across various industries. Key applications include:
- Consumer Goods: Custom plastic insert molding is ideal for creating consumer products, leveraging its benefits for both functional performance and aesthetic appeal.
- Medical Devices: For medical applications, ensure that the plastic used is biocompatible. Insert molding is commonly employed for producing medical implants and other critical devices.
- Aerospace and Automotive: This process is utilized for manufacturing components such as screwdrivers, scissors, dials, and knobs, benefiting from the strength and durability of the molded parts.
- Communication Devices: Insert molding is also relevant in the aerospace and automotive sectors, providing robust and reliable components for communication devices.
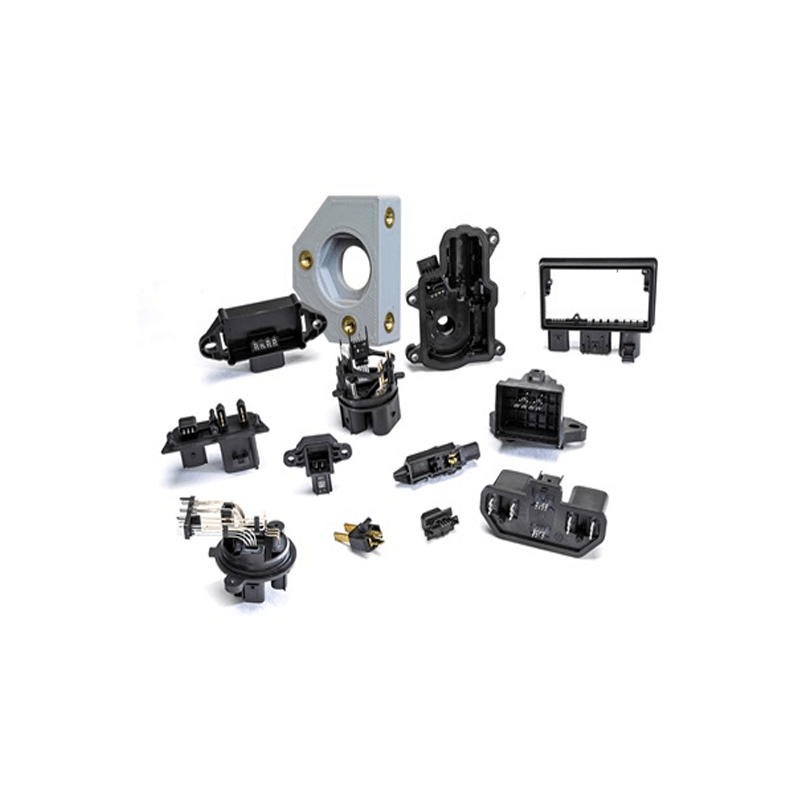
Ready to Request a Custom Insert Molding Quote? (Click here to send an email)
Insert molding is a crucial manufacturing process with extensive applications across various industries, offering numerous advantages. At Lsrmold, we are a full-service custom injection molding provider specializing in high-performance engineered thermoplastics. Our advanced automation and molding equipment enable us to deliver competitive solutions on a global scale.
Contact us today to explore our insert molding services in detail or to request a quote and begin developing your custom solution.