The Introduction of Secondary Processes
Secondary processes, also known as post-processing or finishing operations, are essential for enhancing and protecting injection-molded plastic parts. These processes can improve functionality or achieve a consistent appearance. Customers have a range of secondary operations to choose from, each tailored to refine their molded products. Our team, with decades of expertise in injection molding, guides clients through every stage—from initial design and molding to the final finishing touches. Key secondary processes for molded parts include painting, welding, post-mold machining, assembly, and packaging.
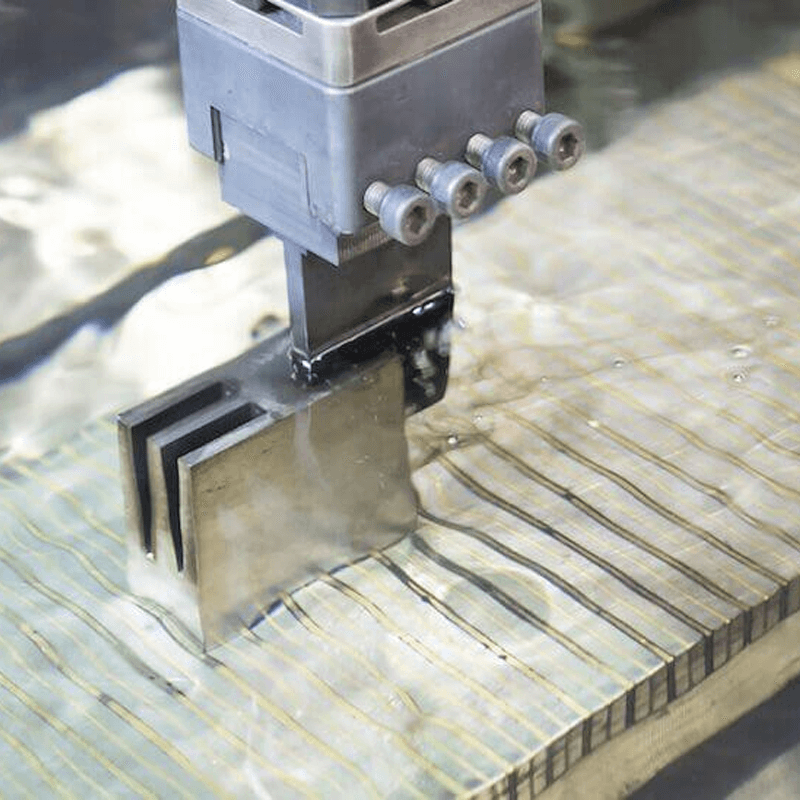
Value-Added Secondary Processes of Plastic and LSR Parts
At Lsrmold, we recognize the significance of value-added secondary processes in elevating the quality and functionality of plastic and LSR (Liquid Silicone Rubber) parts. These processes extend beyond the initial molding stage, enabling us to tailor products to meet specific requirements and deliver enhanced performance.
Value-Added Secondary Processes for Plastic Parts:
Painting and Surface Treatment: Our expertise in painting and surface treatments allows us to enhance the appearance, durability, and corrosion resistance of plastic parts. Custom color options and protective coatings ensure the final product aligns with your vision.
Welding and Joining: We employ advanced welding techniques to seamlessly join plastic components, ensuring structural integrity and eliminating the need for additional fasteners. This enhances both aesthetics and functionality.
Post-Mold Machining: Precision machining after molding enables us to achieve intricate geometries, tight tolerances, and optimal fit. This process is particularly valuable for creating complex plastic parts with demanding specifications.
Assembly and Integration: Our assembly capabilities ensure seamless integration of various plastic components into a cohesive and functional unit. This streamlines production, reduces assembly time, and enhances the end-user experience.
Packaging Solutions: We offer tailored packaging solutions that safeguard plastic parts during transit and storage, maintaining their integrity until they reach their destination.
Value-Added Secondary Processes for LSR Parts:
Overmolding: Leveraging our expertise in overmolding, we can encapsulate LSR parts with other materials to achieve enhanced functionality, improved grip, or added protection.
Surface Texturing: Our precision surface texturing techniques add grip, aesthetics, and tactile appeal to LSR parts, enhancing user experience and usability.
Silicone Printing: We offer customized silicone printing options, allowing for branding, labeling, or adding essential information directly onto LSR parts.
Post-Curing: Through post-curing, we optimize the physical properties of LSR parts, ensuring consistent performance and extending their service life.
Assembly and Sub-Component Integration: Our assembly capabilities enable us to integrate LSR parts into larger assemblies, reducing production complexity and ensuring seamless compatibility.
Quality Inspection and Testing: Rigorous testing and inspection procedures, including dimensional checks and functional testing, guarantee that LSR parts meet the highest quality standards.
Incorporating these value-added secondary processes into our plastic and LSR part manufacturing allows us to deliver products that exceed expectations in terms of performance, aesthetics, and functionality. Our commitment to excellence ensures that each part leaving our facility is optimized to meet your unique requirements.
Secondary Processes for Molded Parts
Enhancing Appearance: Painting
Elevate the visual appeal of your molded parts efficiently through advanced painting techniques. Options such as spray painting and powder coating are available, with the choice of method depending on the chemical properties of the molded material and the desired final application.
Precision Bonding: Ultrasonic Welding
Utilize ultrasonic welding to achieve precise, robust bonds between molded parts. Lsrmold employs high-frequency sound waves to generate heat at the molecular level, effectively melting and fusing thermoplastic materials for a strong, reliable bond.
Robust Joining: Hot Plate Welding
For complex or large molded components, hot plate welding provides exceptional weld strength and precise temperature control. By melting the surfaces of thermoplastic parts, this method ensures a secure and durable join, ideal for intricate assemblies.
Functional Integration: Heat Pressing
Incorporate functional elements such as metal inserts into your molded parts through heat pressing. This technique applies heat and pressure to embed metal components, seamlessly integrating them into the plastic structure.
Mechanical Locking: Heat Staking
Achieve secure mechanical bonds between molded components with heat staking. This process involves inserting a plastic stud from one part into a corresponding hole in another, then applying heat to deform the stud and create a strong, locked connection.
Refining Precision: Secondary Machining
Enhance the precision of your molded parts with Secondary CNC machining. This process removes excess material, refines shapes and textures, and prepares parts for further finishing or assembly, ensuring the highest quality standards are met.
Custom Graphics and Branding: Pad Printing & Screen Printing
Add custom graphics, branding, or identification to your molded parts using pad printing or screen printing. Screen printing is ideal for applying multi-color designs to relatively flat surfaces, while pad printing offers greater flexibility for placing graphics on various part geometries.
Seamless Assembly
For projects requiring assembly, Lsrmold provides comprehensive services, ensuring your molded parts are fully assembled and ready for immediate use upon delivery. We handle the entire process, allowing you to focus on other critical aspects of your project.
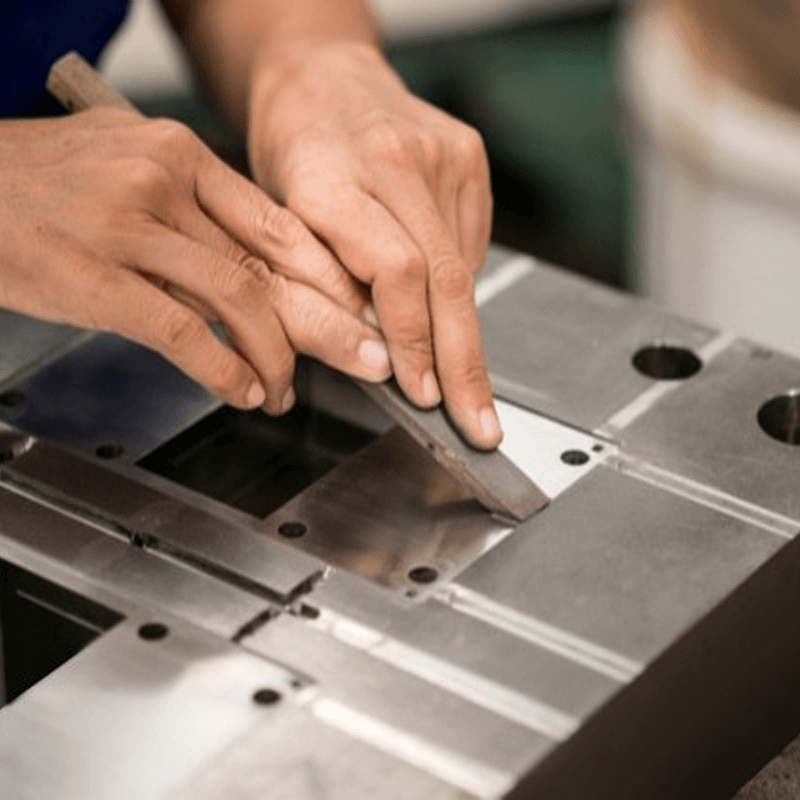
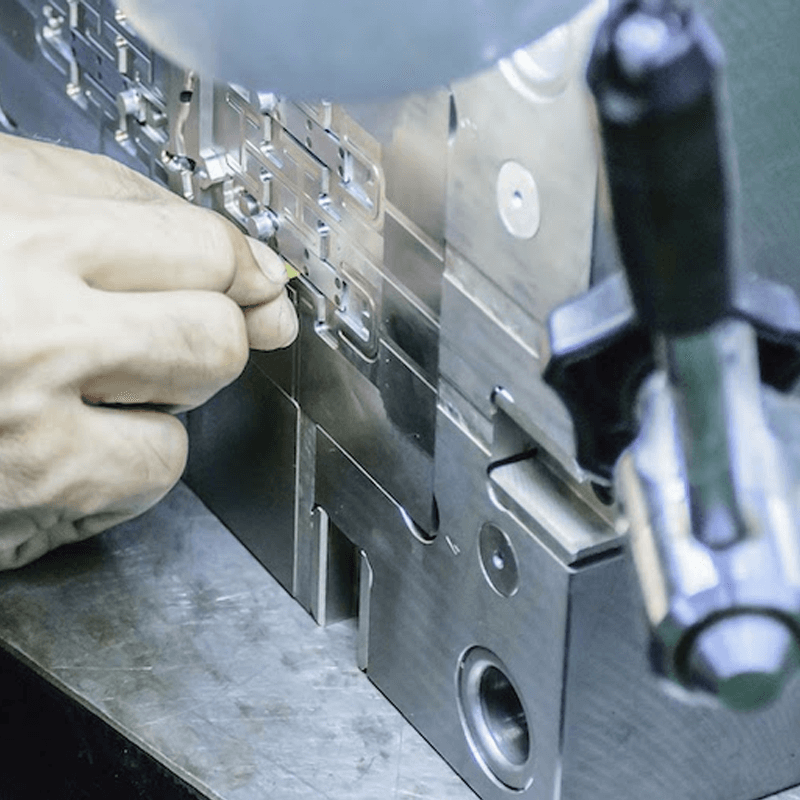
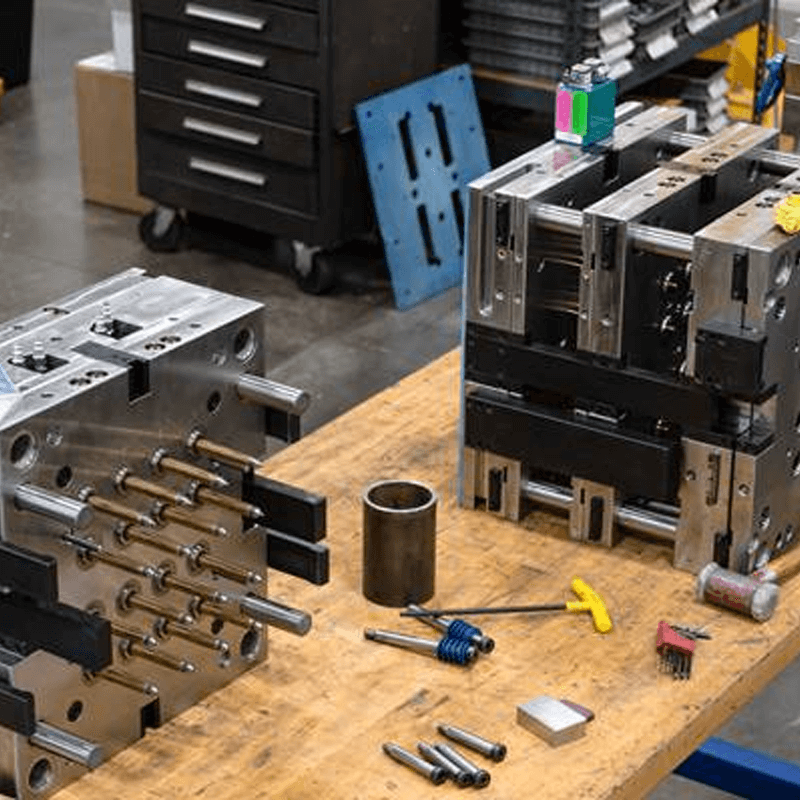
Secondary process for silicone parts
The Secondary process plays a pivotal role in refining and enhancing the performance, aesthetics, and functionality of silicone parts. These essential secondary operations ensure that the final silicone components meet the highest standards and specifications. At Lsrmold, we offer a comprehensive range of Secondary processes tailored to optimize the quality and value of your silicone parts.
Surface Finishing: Painting and Coating
Achieve a flawless and captivating appearance for your silicone parts through precision painting and coating techniques. Our experts meticulously apply specialized paints and coatings to enhance visual appeal, provide protective layers, and ensure resistance to environmental factors.
Precision Bonding: Ultrasonic Welding
Harness the power of ultrasonic welding to create robust and reliable molecular bonds between silicone components. Our advanced ultrasonic welding process utilizes high-frequency vibrations to fuse silicone parts seamlessly, ensuring structural integrity and long-lasting performance.
Functional Integration: Insert Molding
Elevate the functionality of your silicone parts through insert molding, where metal or other materials are integrated within the silicone structure. This process enhances versatility, allowing for the incorporation of features like threaded inserts or metal reinforcements.
Customized Graphics: Printing and Marking
Enhance brand visibility and product identification with precise pad printing and marking techniques. Whether for branding, labeling, or essential information, our printing solutions offer clear and durable graphics that withstand environmental challenges.
Assembly and Packaging
Ensure a streamlined production cycle by leveraging our assembly and packaging expertise. Our team can seamlessly assemble silicone components and package them to your specifications, ensuring they are ready for immediate use or distribution upon delivery.
Quality Inspection and Compliance
Every silicone part undergoes meticulous quality inspection to ensure it meets the highest industry standards. Our rigorous quality control processes guarantee that each component meets its intended specifications and complies with relevant regulations.
Why Choose Lsrmold for Secondary Processes of Your Molded Parts?
Material Expertise: Lsrmold brings extensive experience with both mold and LSR (Liquid Silicone Rubber), allowing us to identify and apply the most effective secondary processes to achieve optimal results for your molded parts.
Precision and Consistency: Our advanced secondary techniques guarantee precise, repeatable outcomes, enhancing the functionality, appearance, and performance of your molded components.
Tailored Solutions: We recognize that each industry and application has unique requirements. Our customized secondary processes are designed to meet your specific needs, ensuring solutions that perfectly align with your project goals.
Cutting-Edge Facilities: Lsrmold is equipped with state-of-the-art facilities and the latest technology, enabling us to perform a wide range of secondary treatments with unmatched efficiency and excellence.
Commitment to Quality: Quality is at the core of everything we do. Our rigorous quality control protocols ensure that your molded parts consistently meet the highest standards throughout the secondary process.
Comprehensive Services: From surface treatments and coloring to assembly and packaging, Lsrmold offers a full spectrum of secondary services, streamlining the production process and saving you valuable time and resources.
Finish Your Mold Parts with Lsrmold
Lsrmold provides a comprehensive range of surface finishes for molds, including SPI-standard surface roughness and aesthetic enhancements like texturing, color matching, and design transfer. Our post-processing services encompass part joining, increased durability, painting, light assembly, and protective packaging, ensuring your molds are both functional and visually refined. Our expert team is dedicated to guiding you through the process, adding exceptional final touches to your project. Contact us today to explore our mold services and discuss your specific needs.